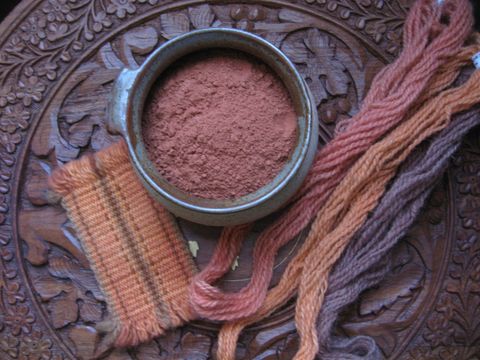
A simple story about Natural Dyes
Would you not like to know how clothes used to get colored before dyes were prepared artificially? Well just going down in History you get to know quite a lot. But before that let us just skim through the methods of dyeing in today’s times and then go back in time awhile, for a better understanding.
Three classes of dyes
There are three class of dyes from the point of view of how a textile receives dye.
Substantive Dyes
One may have noticed that using turmeric as a dye, both the dye bath and the fabric become orange – yellow. Similarly with greenish yellow staghorn moss, as the dye begins to simmer color is taken up by the textile. These two dyes belong to the class of dyes known as direct or substantive. When a dye substance is soluble in water and is taken up directly, it is a substantive dye.
Mordant Dyes
The second class of dyes is known as “mordant” dyes. Most natural dyes belong to this group. A dyestuff which cannot be fixed on the fiber, without the use of chemical assistants is known as mordant dye. A mordant is a chemical which combines with the dye within the fiber. Examples of mordant dyes are alum, chrome, iron, tin and copper salts.
Vat Dyes
Vat dyes are the third class of dye and rare in nature. The crude vat dye is insoluble. It must therefore be acted upon by either bacteria or chemicals and reduced to solubility. When a textile is immersed in the solution and then exposed to air, the dye is oxidized and fixed permanently on the fiber. No wonder vat dyes are lightfast and wash fast. The magnificent Tyrian purple and indigo are examples of this dye class. Even though vat dyeing is demanding it is within the home dyer’s capability.
Another helpful way of grouping dyes is by their origin or source. From the point of view of source, dyes are either artificial or natural. Among the natural sources of dyes, are plants, animals and minerals.
Tyrian purple from mollusks, and reds and scarlets from the female kermes, lac and cochineal insects. Tea in an iron pot and Iron buff demonstrate the use of mineral coloration.
Historical background
Natural dyes were the only source of dyes until 1856. Sir Henry Perkin quite by accident discovered a mauve colored coal tar product which he named as ‘mauvine’ (He had been attempting to synthesize quinine). This was the beginning of the artificial dye industry. Gradually natural dyestuffs were discarded. Finally with the synthesis of an indigo blue substitute in production in 1900, natural dyes became a part of the past.
It is important to point out the accidental aspect of Sir Henry’s discovery. Natural dyes were doing the job. Recipes had been refined over thousands of years. The art of dyeing was highly developed. The colors were fast, as bright as anything known of and cheap.
Chemists were not concerned with textile colors because the old dyes were serving nicely and dyeing was not yet a science. Old dyes represented 6000 years of trial, accidental discovery and involved refinement. All this was lost by the accidental discovery made the industry turn to the use of artificial dyes. Not only did we lose the technology of natural dyeing, but we also lost contact with still another home art and our self-esteem. (It does give you self-esteem to know that you can go outdoors, collect a pot full of weeds, brew a dye and color your shirt in the brew.
Ancient writers write that there were a thousand and odd different natural sources of dye. As trade in dyestuffs improved in the ancient world, there evolved a limited group of dyestuffs considered desirable. When trade routes opened up in the sixteenth century these dyes became available to European dyers.
The types of dyes in use in Europe until the discovery of the artificial Mauveine were a highly selected group. They were all imported from the Near East and South America. You could refer to them as “imported” or “exotic” dyes as contrasted to dyes from local North American plants. The most efficient dyes were the exotic dyes. The professional or home dyer of the early 1800s had about twenty or so dyestuffs that he could use. Of these there were nine that were considered the most practical.
They were: indigo and woad blue, cochineal and madder red, logwood black, fustic, weld, safflower and saffron yellow. Of these logwood is the only dye still being used commercially. (It is used for black on silk and nylon). The others available in limited amounts and could usually be purchased from shops selling hand weaving and spinning supplies. Are the exotic dyes worthwhile? Yes they are our most reliable source of natural dye. However they are costly. Let us talk of the most important four. Indigo, woad, cochineal and madder.
Indigo
Indigo is still considered as one of the most important in Asia, and for more than 4000 years considered a cosmetic and dye. Dye from the leaves of this plant yielded a beautiful blue on wool and cotton. Further it was notably fast to light and water, and this double fastness was considered an unusual quality. When early dyers were seeking blue, indigo became the perfect answer, since blue sources were scarcely found in Nature. Its quality therefore made it a valuable trade item. This dye belongs to the special lot of dyes known as vat dyes and was used commercially right upto the early part of the twentieth century. It was the last of the natural dyes till synthetic or man-made dyes took over.
Today it is found only in India, its place of origin and is used to color the hair. Because the process of preparing the dye is very elaborate – tedious, odorous and demanding, one could try powdered or lump indigo as an experiment.
Woad (Isatis tinctoria)
It was the source for the blue color in Europe till the 17th century. The plant is a member of the mustard family and like mustard was accustomed to cold climates. The coloring principle derived from the leaves is indigotin as in the indigo plant, but is of much less concentration. Woad is also a vat dye and is fast to light and washing. A historian talks of ancient Teutons darkening their grey hair with Woad, though it seemed a ghastly sight.
Also the ancient Celts were called “Picts” meaning “painted people” because they pierced their skin with flint tools and darkened the ‘designs’ with woad dye. For centuries woad was of great importance in trade to Europe because indigo comparatively was costlier. Even after sea trade was established with India, the woad trade was backed by local governments with laws favouring them. In England, the use of indigo carried penalties as late as the seventeenth century. In Germany, where woad was commonly grown, anti-indigo laws were common. In France, cloth dyers were not given ample freedom to use indigo till 1737. In fact the free use of indigo was delayed by more than 250 years. Just like indigo, the extraction of color from woad is a very cumbersome process.
Cochineal plant dye sources are almost as scarce as blue. No wonder these two sources have also been valued for centuries. The brightest reds were of animal origin. Dyes were extracted from four types of beetles (Coccidae). The kermes beetles live on oak and the cochineal beetles live on cactus and grass. The dyes are brilliantly red and scarlet and remarkably lasting. Pliny referred to these reds and Tyrian purple as luxury colors. These were indeed costly colors with one insect furnishing a droplet. Therefore only the very rich could afford them. Of all the sources of red, cochineal found on opuntia cactus became the most used. This had been discovered in great quantities by the Spanish conquerors in Mexico who extorted and exported it to Europe.
The Aztecs collected the beetles by brushing or scraping them off the cactus. The beetles were killed by immersing them in boiling water or vapour. Synthetic alizarin came into wide use for coloring red in 1880.
Madder (rubia tinctorum)
The madder plant is such an ancient and excellent source of the color red that its name means red in several languages. In Latin it is rubia, in German it is rote. Coffee, quinine, dyes and medicines are all derived from this family. The dye, the mordant type, is derived from the root of the plant that is as slender as a pencil.
In Europe Madder became a plant of economic importance. Charlemagne the emperor got it cultivated on his estates to encourage farmers to grow it. In fact in Holland in the fifteenth, sixteenth and seventeenth centuries it had great importance as a cash crop. By 1782, France had become the top grower of Madder in Europe. In between during the French Revolution, Madder farmers were ruined, but with Louis Philippe’s decree of having red caps and trousers for his army, that saw its encouragement, it again revived.
In England the army uniforms were colored with imported red (Redcoats). Until 1869, England’s Madder imports came to 1 million pounds sterling. In 1869, the world production of 70000 tons came to 0. Why? Because artificial Madder dye was synthesized with fields upon fields of farms lying vacant and farmers eyeing desolation. Thus came the downfall of a great coloring dye with the natural dye being replaced by a synthetic one. Madder seems gone and replaced by a herb sweet woodruff.
A little about Vat Dyeing
Vat dyes are spoken of as dyes that are insoluble in water. While mordant dyes are soluble in water on application of a little heat, vat dyes do not become soluble even when the water is heated. For such dyes, the reduction process is adopted whereby a special chemical must be allowed to act upon the insoluble dye. The result is a colorless, soluble substance called indigo white. At this stage a textile is immersed in the vat and then aired. The exposure to the air turns the textile blue. (The indigotin is oxidized). The blue once again gets insoluble and is fixed in the fibers of the textile.
The question therefore is – how does one get the indigo to become soluble and act as a dye?
The process of reduction involves a process called steeping wherein a substance is added and let remain for several days that provides the alkalinity and nitrogen to cause microbial fermentation and thereby making the indigo soluble. Since the entire process is carried out in specially made vats, reduction dyeing is also known as vat dyeing.
As Vat dyes characteristically require a reducing agent to solubilize them, the most common reducing agent is sodium dithionite (Na2S2O4), which converts the dye to its "leuco" form that is soluble. Once attached to the fabric, the leuco dye is then oxidized to the insoluble state which is intensely colored.
Chemical reactions such as oxidation, reduction, pH control are often necessary; even the dissolution process necessitates measuring out appropriate quantities of caustic soda and sodium hydro sulphite in order to achieve reduction. The dye is soluble only in its reduced form. The fiber is immersed repeatedly in this oxygen-free dye bath then exposed to the air, whereupon the water-soluble reduced form changes color as oxygen turns it to the water-insoluble form. For these reasons, vat dyes are less suitable than fiber-reactive dyes for amateur use. Indigo is an example of this dye class: it changes from yellow, in the dye bath, to green and then blue as the air hits it. Not all vat dyeing is done with vat dyes.
Properties of Vat dyes
- The vat dyes have high color fastness, which is uncommon in other dye classes.
- On the other hand, vat dyes tend to have poor rubbing fastness, but this can be mitigated with special treatments to the fabric.
- Indigo is subject to major crocking (i.e., rubbing the dye off onto other items) unless it is applied carefully. This means that dipping many times in a weaker dye-bath is more preferred than to dip once in a stronger dye-bath
This story does not have an ending. Just a progression with time because till Man exists, he will need to cover himself. What he covers himself with, needs color, since he has always liked a colorful front to create an impression. What could probably change is what he wears or the manner in which the color is applied.