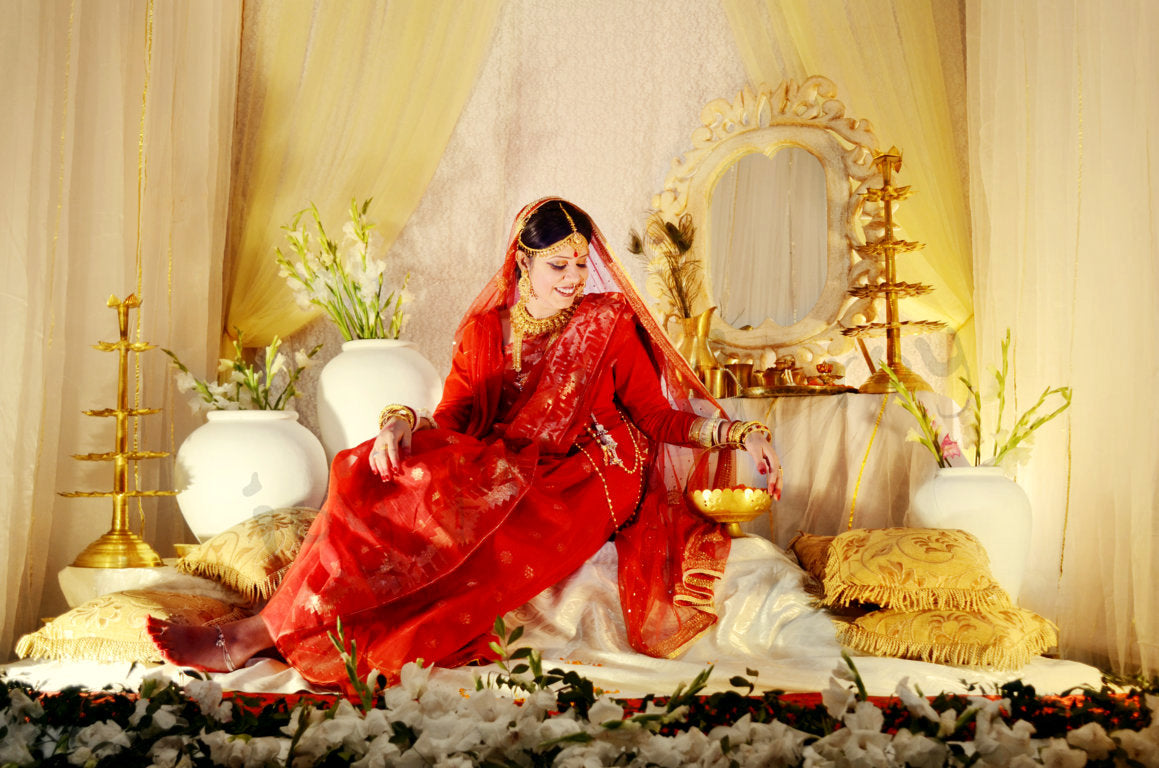
Jamdani – a fine art weave attachment on fabrics – Part II (In continuation of Part I)

Jamdani has its roots in Dhaka, Bangladesh that later took on the form of a fine art of weaving in present day Bengal. The fine cotton fabric is deftly embellished with intricate motifs that are expertly woven into the fabric. The Jamdani weaving tradition is one of the most time and labor intensive forms of hand loom weaving. Intending to improve the aesthetic appeal, it takes the form of cotton and gold thread work to create motifs of geometric patterns and floral designs in colourful hues.
Some of the traditional motifs include Chameli–Jasmine and Gainda buti-marigold. The most attractive design feature of the jamdani sari is the paisley motif. The Jamdani is a method by which the design motifs are added by hand during the course of the weaving, thus resulting in an embroidery effect. The method of production is somewhat similar to tapestry work. Small shuttles filled with coloured, gold or silver thread, are passed through the warp as required during the actual weaving of the basic fabric. There are several kinds of Jamdani muslins.
- Natural-coloured, unbleached cotton grounds with bleached white cotton supplementary work are traditional,
- pastel-coloured grounds with white supplementary work and dark-coloured grounds (black, dark blue and dark red) with white supplementary threads are modern innovations.
- Any of the above with coloured supplementary threads, or dark grounds with only zari supplementary work are also seen.
Paper patterns are generally not used. As a rule two weavers sit at the same loom to save time and simplify the intricacy of the weaving process.
Traditional jamdanis are made in Tanda in Uttar Pradesh. Finely patterned white jamdanis have been made there since the 19th century. White on white patterning woven with a thicker thread distinguishes Tanda jamdani dopatta . The most exclusive of these delicate muslins were those that had a distinctive style of discontinuous supplementary weft work woven into the fabric, usually in red and black. This creates opaque patterning against a transparent ground. Two weavers usually weave Jamdani on a simple handloom, one adding each supplementary weft motif by hand using individual spools of thread. No warp-lifting mechanisms such as those of a draw loom are necessary, although it makes this labour intensive fabric prohibitively expensive. In 1903, when a silk sari cost as little as 5 rupees, a jamdani sari fetched 500 rupees.
Jamdani weaving is labour intensive, requiring a delicate touch. Seated at the loom, the master and his assistant weave patterns with colour or metal thread, once guided by designs on paper but now by verbal instructions. The jamdani work is essentially tapestry work, the wefts forming the pattern where needed, being threaded through the warps with a wooden or bamboo needle. By using thread as fine as the compound weaves, the weft patterns seem to merge and float within the cloth, rather than appear as an overlay or woven decoration.
[/vc_column_text][/vc_column][/vc_row][vc_row][vc_column][vc_column_text]The Jamdani process
Most of the weavers are Muslims who believe figurative representations in art are a direct challenge to the omnipotence of God. For this reason, artisans create motifs drawn from nature or abstract designs with a geometric sensibility. Pit looms are still used, however, the original throw shuttle has been replaced by the fly shuttle, a faster and more efficient method of production that still depends upon the hand for guidance. Traditionally, the plain weave background was white, off-white or grey; today background colors are chosen from a vibrant array. The best quality jamdani is produced with locally grown, fine cotton. It is always woven during the monsoon season from June to October when the air is humid and moisture prevents the fine threads from becoming brittle and breaking. Bundles of thread are dyed in a variety of colors.
The dyed thread is strengthened and softened by soaking overnight in a solution of rice water starch, allowing the women to wind it more easily onto bobbins. It is tedious work done early in the morning, usually between 4 and 9, before the increasing heat dries the thread, making it more difficult to handle. The wound bobbins are sent to another worker who prepares the warp on a beam. Afterwards, the warp is sent to the weaver’s house where it is set up on a loom. Drawings are placed under the warp as a guide. The weaver, almost always a man, may or may not follow the drawing, often preferring to work from intuition alone. Colored thread is carefully inserted and hand tied into the fine weft to create patterns on the plain weave.
[/vc_column_text][/vc_column][/vc_row][vc_row][vc_column][vc_column_text]
The entire system of production, from dyeing the thread to setting up the loom, is determined by the length of jamdani’s most marketable end product, the sari. For this reason, it is nearly impossible to convince weavers to produce different lengths of running yardage. Looms are set up with 11 meter warps, each warp yielding two saris, 5.5 meters in length. The patterns woven into these two saris will not be repeated by the weaver again.
The first step is to inventory and catalogue the material, sorting the scraps by color and size. To create new yardage, larger remnants of plain, pattern-less jamdani are joined to make a 4-meter base cloth, onto which smaller, patterned scraps are positioned and pasted in place. Designs are hand drawn in pencil onto the patterned pieces then carefully cut out along these lines exposing the base cloth underneath. The cut edges are turned under and hand appliquéd, adding a layer of textural interest to layers of transparency in the fabric.
[/vc_column_text][/vc_column][/vc_row][vc_row][vc_column][vc_column_text]
Buy online Jamdani cottons from Unnati Silks
The bengal handloom cotton saree with green self checks all over accompanied by zari and plain borders and cream stripes and zari adorned pallu is a rich looking stunner that would suit a variety of occasions like parties, weddings, social functions, corporate events and festivals.
Baluchari sarees, shantipur saris, Bengal cotton sarees and tussar silk saris of jamdhani pattern woven in highly mercerized cotton and silky thread are famous jamdani weaves of West Bengal. These classic weaves are well apt for daily casual, corporate conferences, college parties and festivals. The Dhakai cotton handlooms and the Rajasthani cottons are fine fabrics for the Jamdhani and the resulting Jamdani cotton handlooms with Jamdani woven decorative motifs, exotic patterns on the pallu, multi-coloured borders make the Jamdani cotton sarees much sought after.
When the Banarasi Sico or the Gadwal handloom fabrics, the Bengal cottons or the Uppada Silks have highlighted motifs or extra rich patterns, a splash of riotous colours or fanciful unique borders, the enhancing hand-weave of the Jamdhani technique is what brings it about. A traditional art of elaborate handiwork, it is much in vogue in fashion fabrics of today.
[/vc_column_text][vc_column_text]
To call the Jamdani merely a manner of weaving would not be correct. To say that it is an adornment for well woven fabrics would only be partially true. To say that Jamdhani is the showpiece of Bengal would just about say a one-sided story. For the Jamdhani is way beyond that. It is an incorporation an emphasized addition, a manner of creating the extraordinary, for once the Jamdani is introduced in a weave, it transforms, it converts, it re-creates, and produces ultimately what seemingly would have been an average creation as a masterpiece of surpassed expectations.
[/vc_column_text][/vc_column][/vc_row][vc_row][vc_column][vc_gallery type="image_grid" images="11052,11053,11054,11055,11061,11056,11057,11058,11060,11059"][/vc_column][/vc_row][vc_row][vc_column][vc_btn title="Online shop for Jamdani Sarees" color="success" link="url:http%3A%2F%2Fwww.unnatisilks.com%2Fsarees-online%2Fby-popular-variety-name-sarees%2Fjamdhani-silk-sarees.html||target:%20_blank"][/vc_column][/vc_row]